7 Common Pallet Rack Protection Mistakes and How to Avoid Them
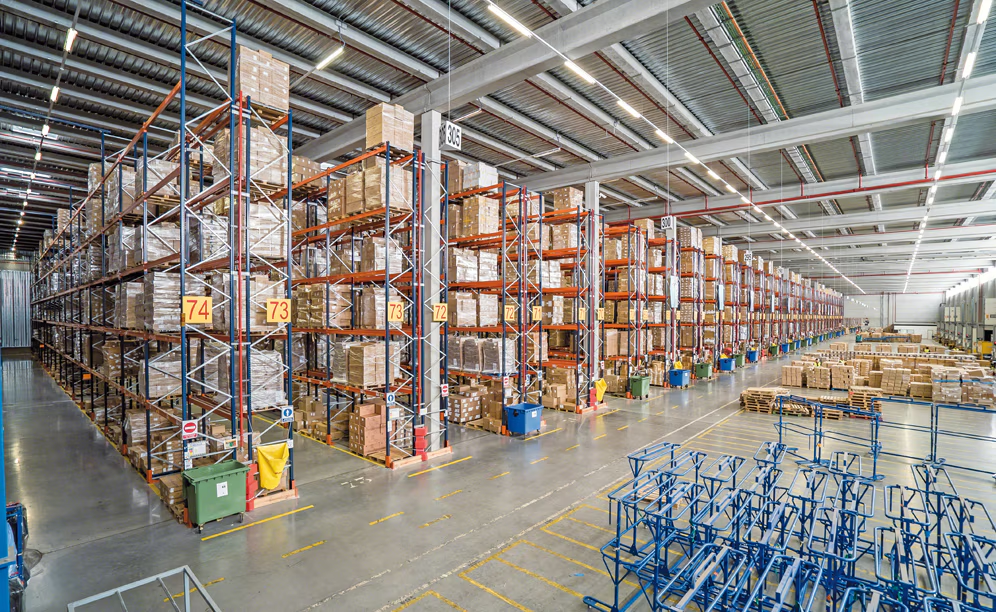
Wheelhouse safety depends on pallet rack protection. If suitable care is neglected, racks may suffer damage that might cause mishaps and costly repairs. Many warehouses neglect to take necessary care to maintain their pallet racks, therefore compromising efficiency and safety. This study investigates the most common mistakes made while safeguarding pallet racks and provides useful tips for avoiding them. By avoiding these problems, businesses may prolong the life of their warehouse racking installation and maintain safer surroundings.
Neglecting Routine Inspections
Pallet racks must undergo routine inspections to remain secure and operational. This activity is often neglected in warehouses, causing minor problems to escalate into serious risks. Over time, pallet racks may develop loose bolts, bent beams, or dents, all of which compromise the rack’s structural integrity. Early detection of these problems through inspection lowers repair costs and prevents additional damage.
Additionally, routine inspections enable warehouse employees to spot and fix wear and tear brought on by daily activities. Setting up inspections on a monthly or quarterly basis guarantees that possible issues are identified before they cause mishaps or delays. Don’t neglect inspections; regular observation maintains pallet rack protection and averts expensive repairs.
Rack Overloading
One of the most common blunders is overloading racks beyond their designated weight limit. When certain limits are exceeded, the rack structure is strained, increasing the likelihood of its collapse. Weight constraints are frequently disregarded in warehouses, particularly during peak hours; however, doing so endangers the rack and its occupants.
Staff should be trained to load racks within their capacity and weight limitations should be clearly marked on each rack to prevent overloading. Supervisors should also keep an eye on loading procedures to guarantee adherence. In addition to protecting racks, keeping weight within safe bounds prolongs their life and eventually reduces replacement expenses.
Not Putting in Column Guards
Column guards are crucial safety devices that shield rack frames from direct strikes. Ignoring this safeguard exposes racks to forklift collisions, which frequently result in rack damage. These guards are especially useful in warehouse settings where forklift activity is common since they lessen damage and absorb shock.
Installing column guards at the base of each rack is a quick and easy solution to mitigate against unintentional hits. Column guards are a necessary component of any pallet racking for sale because they are also reasonably priced and simple to install.
Putting Racks Too Near to One Another
A common mistake that restricts forklift and employee maneuverability is leaving little space between racks. Close spacing makes it more likely that unintentional impacts will damage racks and inventory. Additionally, workers find it more difficult to efficiently access and arrange inventory when there is a lack of room.
To prevent this, keep the aisles sufficiently wide for forklifts to operate securely. Arrange the warehouse so that there is no chance of a collision and that every rack is easily accessible. Properly spacing racks reduces rack damage and produces a safer, more effective warehouse environment.
Ignoring Floor Anchoring
Some warehouses overlook the crucial safety precaution of fastening racks to the floor. Floor anchors stabilize racks, lessening the possibility that they will topple over when subjected to large loads or hits from forklifts. Racks without floor anchoring are more prone to damage and movements, particularly in high-volume storage settings.
Each rack should have floor anchors installed to provide stability during normal operation. Additionally, as the stability of racks may be strengthened most simply during warehouse racking construction, make sure anchor placement is correct.
Ignoring Adequate Distribution of Loads
Uneven load distribution increases the chance of structural collapse by placing unnecessary stress on particular rack parts. Racks can become unstable and bend or even collapse if too much weight is placed on one side or high up on them. On the other hand, the rack remains balanced and any strain on any one section is reduced when the weight is distributed properly.
Teach employees to distribute weight throughout rack levels uniformly and to put heavier products at the bottom. Additionally, ensure that loading procedures adhere to these rules regularly. In addition to maintaining rack stability, even weight distribution maximizes the available area for more effective storage.
Making Use of Incompatible Racking Elements
Racks’ structural integrity may be jeopardized if multiple brands or types of racking components are used together. Incompatible parts can result in poor stability and a higher chance of failure because not all components are made to function together. Warehouses frequently make this error when they extend storage or fix racks without taking compatibility into account.
To avoid this error, use the parts that the rack manufacturer recommends or speak with a racking specialist. Additionally, keep extra appropriate components on hand to make maintenance and repairs easier.
In Conclusion
Latest Blogs
How Modular Cabinets Enhance Warehouse Inventory Control
For more flexibility and management in your warehouse, discover how modular cabinets can improve workflow and inventory control with these features.
How Modular Cabinets Enhance Warehouse Inventory Control
For more flexibility and management in your warehouse, discover how modular cabinets can improve workflow and inventory control with these features.
Important Questions To Ask Before Hiring Mezzanine Builders
To achieve a layout that boosts work productivity, find out what kind of questions you should ask your mezzanine builders before they work in your warehouse.
Effective Strategies for Efficient Pallet Rack Installation
To optimize your warehouse layout, discover how to efficiently install a pallet rack system that maintains and improves work performance across your business.
Questions?
Let’s Chat About Your Warehouse Project Today!
Or all us at 515-635-1555
Save time. We will contact you
Provide your details, and we’ll help you find exactly what you need