Choosing the Right Vertical Lift Module for Your Warehouse
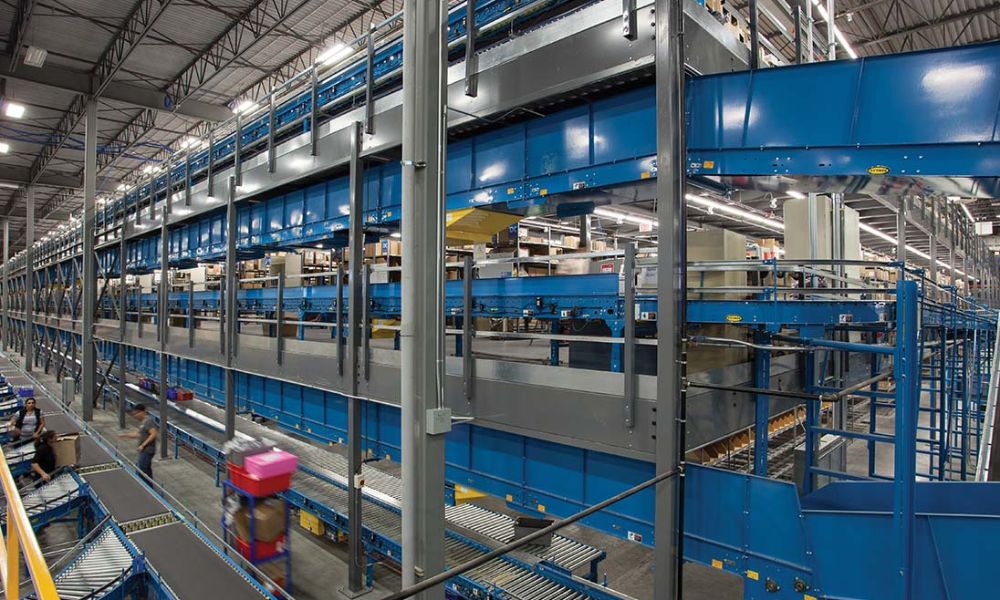
Selecting a vertical lift module (VLM) for your warehouse directly affects your operational efficiency, storage capabilities, and productivity. A VLM optimizes storage space by utilizing vertical height, allowing you to store items in a compact and organized way. By increasing accessibility and reducing retrieval times, a VLM can improve workflows in your warehouse.
However, with the wide variety of VLM systems available, choosing the right vertical lift module for your warehouse can be tricky. Luckily, you can simplify the search when you know how to navigate the decision-making process.
Assess Your Storage Needs
Start by analyzing the items you plan to store in the VLM. Are you dealing with small and lightweight components, large and heavy products, or both? Understanding the dimensions, weight, and quantity of your inventory is crucial for selecting a VLM that meets your needs without requiring modifications.
Consider whether you’ll need specialized trays, dividers, or compartments to keep items secure, organized, and accessible. Outlining your storage requirements encourages you to invest in a system that fits your operations, improves efficiency, and doesn’t waste space.
Evaluate Available Space
Measure the vertical height and floor area in your warehouse to determine where the VLM will fit. While VLMs maximize vertical storage, it’s important to confirm that your facility has sufficient ceiling height and floor space for installation and operation. Also, account for overhead obstructions, such as beams, light fixtures, and sprinkler systems.
Consider the space around the VLM; operators need adequate room to access the system and ensure smooth workflows and safety in the surrounding area.
Weight Capacity
Carefully assess the weight of the items you plan to store in the VLM. Each system has a maximum load capacity, and exceeding this limit can cause breakdowns, safety hazards, or costly damage. Select a VLM with a buffer above your heaviest load requirements so that the system can handle inventory safely and efficiently. If your inventory consists of items with varying weights, look for a system that can balance heavy and light loads across different trays to optimize performance.
Speed of Retrieval
Consider how quickly your team needs to access items in the VLM. In fast-paced environments, retrieval speed can affect productivity. High-speed VLMs with advanced automation or dual tray systems can reduce order picking and restocking times.
VLMS are particularly important during peak periods when delays can negatively affect operations. Evaluate your workflow, and determine whether a faster system is worth the investment to keep up with your team’s demands.
Automation Features
Modern VLMs offer a range of advanced automation features, such as automatic picking, integrated inventory tracking, and compatibility with barcode or RFID systems. These features eliminate manual processes, reduce human error, and improve efficiency.
For example, automated systems can provide real-time inventory updates, allowing you to track stock levels and reorder items. Evaluate whether these automation capabilities align with your current operation and future growth plans, as they can streamline your workflows.
Ergonomic Design
Operator safety and comfort should be a top priority when selecting a VLM. Look for systems with ergonomic features, such as adjustable workstations, user-friendly controls, and accessible trays. Reducing physical strain on your team not only enhances productivity but also minimizes the risk of workplace injuries.
Scalability
Think about your warehouse’s future growth potential. With a scalable VLM, you can expand your storage capacity or adapt the system as your operational needs evolve. For example, if you will be adding new product lines to your business, a scalable system can accommodate those changes without needing costly replacements or upgrades. Investing in a scalable system guarantees long-term value, helping you avoid unnecessary expenses down the road.
Software Compatibility
The VLM’s software should integrate seamlessly with your existing warehouse management system (WMS) or enterprise resource planning (ERP) software. Integration can simplify inventory tracking, order processing, and reporting and create a more streamlined operation. Additionally, look for software that offers real-time analytics and user-friendly interfaces to maximize efficiency and help your team make data-driven decisions.
Energy Efficiency
Energy-efficient VLMs can help you lower operational costs while supporting your company’s sustainability goals. Look for systems with energy-saving features, such as eco-friendly motors, standby modes, or LED lighting, to reduce electricity usage during downtime.
Over time, these features can lead to cost savings, especially in facilities where the VLM operates continuously. Additionally, opting for an energy-efficient system can demonstrate your company’s commitment to environmental responsibility.
Maintenance Requirements
Review the maintenance needs of the VLM you’re considering. Systems with minimal upkeep requirements are less likely to disrupt operations, saving you time and money. Research the availability of replacement parts, average frequency of maintenance, and whether the manufacturer offers support services.
Some vendors provide predictive maintenance options; sensors monitor the system’s performance and alert you to potential issues before they worsen.
Vendor Reputation
Research potential vendors and manufacturers thoroughly before making a decision. Choose a provider with a good reputation, proven expertise, and reliable customer service. Also, look for testimonials, case studies, and reviews from other businesses to gauge the vendor’s reliability and track record. A trusted vendor not only delivers a quality system but also provides ongoing support so that your VLM operates smoothly over its lifespan.
Budgeting
Determine your budget and calculate the total cost of ownership, including installation, training, operation, and maintenance costs. While it may be tempting to go for the cheapest option, it’s important to weigh cost against quality, features, and long-term usability. A slightly higher upfront investment in a reliable, feature-rich VLM can pay off through improved efficiency and reduced downtime.
Warranty and Support
Examine the warranty and technical support options offered by the vendor. A comprehensive warranty can save you from unexpected repair costs, while responsive technical support resolves issues. Look for vendors that offer extended warranties or service packages so that your system remains operational for a long time.
Choosing the right vertical lift module for your warehouse is a game-changer for your warehouse operation. When you enhance productivity, conserve space, and support long-term growth with your VLM, you take the efficiency of your business to the next level.
A thoughtful investment today can provide long-lasting improvements to your warehouse efficiency in the future. Midwest Warehouse Solutions can help with our material handling equipment solutions. With us on your side, your business will be ready to meet future challenges!
Latest Blogs
How To Maximize Productivity With Workstation Bridge Cranes
Looking to boost productivity amongst your staff? Improve your warehouse’s work environment by implementing workstation bridge cranes with these tips.
How To Maximize Productivity With Workstation Bridge Cranes
Looking to boost productivity amongst your staff? Improve your warehouse’s work environment by implementing workstation bridge cranes with these tips.
How Modular Cabinets Enhance Warehouse Inventory Control
For more flexibility and management in your warehouse, discover how modular cabinets can improve workflow and inventory control with these features.
Important Questions To Ask Before Hiring Mezzanine Builders
To achieve a layout that boosts work productivity, find out what kind of questions you should ask your mezzanine builders before they work in your warehouse.
Questions?
Let’s Chat About Your Warehouse Project Today!
Or all us at 515-635-1555
Save time. We will contact you
Provide your details, and we’ll help you find exactly what you need